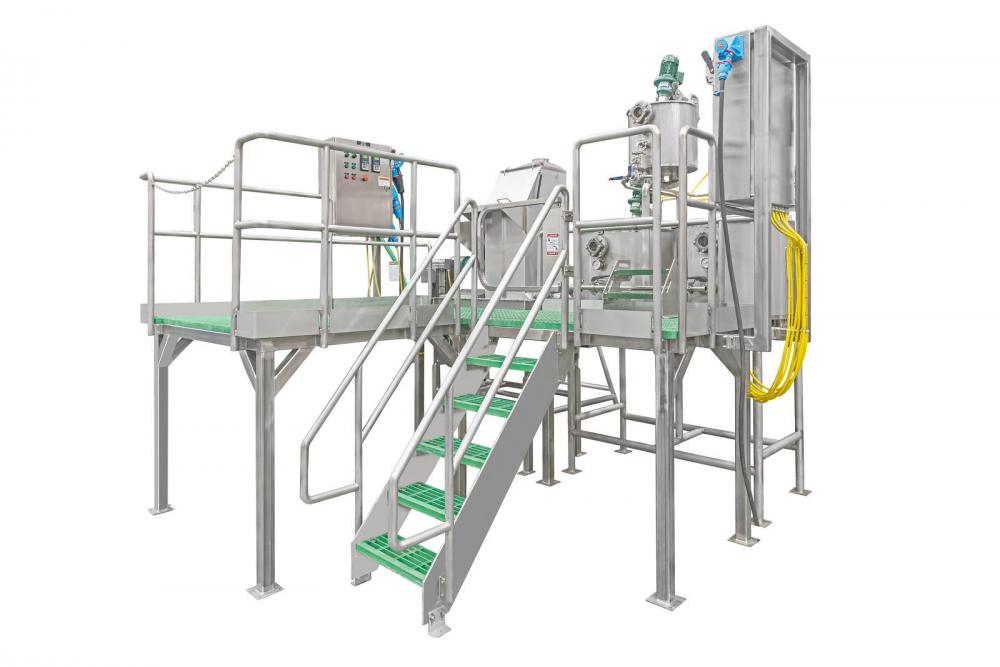
Custom Processing Equipment will Improve Production of Ready-to-Use Therapeutic Food in Côte d’Ivoire
Over 2 billion people around the world don't get adequate amounts of micronutrients in their diets like iron, vitamin A and zinc. Nutrient deficiencies can lead to stunted growth and life-long cognitive impairment in kids. Africa alone has the highest prevalence of undernourishment, with 20% of its population being affected. An important part of the PFS mission is to work with African food processing companies who provide healthy foods that support improved nutrition.
Project Peanut Butter (PPB), a nonprofit organization that seeks to advance the treatment of severe malnutrition through ready-to-use therapeutic food (RUTF) is one such client. RUTF is a nutrient-dense, locally produced peanut butter paste used for the treatment of severe acute malnutrition in children. PPB currently serves communities in Ghana, Malawi and Sierra Leone, and is expanding its operations to Côte d’Ivoire.
Partners in Food Solutions (PFS) and Project Peanut Butter have been working together since 2012 and have partnered on over 40 projects. Perry May, who retired from General Mills in 2015, has been volunteering on PPB projects since 2012 and has seen the impact of their work. “I really enjoy working with PPB. I’ve been involved with many of their projects and have seen a lot of business growth over the years and have even visited a PPB plant in Malawi. One of the current projects I am most excited about is their expansion project in Côte d’Ivoire,” Perry said.
With a new facility in Côte d’Ivoire, PPB will be able to reach a new population of people they didn’t have the opportunity to serve before. For the new plant, PPB was looking for recommendations to source a new piece of equipment to process their RUTF products.
After multiple discussions between PFS volunteers and PPB, they selected Anderson Dahlen Inc. (ADI), a custom design and manufacturing equipment builder based in Ramsey, MN, to design and build a RUTF processing system. “The reason we recommended them for the RUTF processing system was because we needed a vendor who had sanitary design for food equipment in mind. PPB was going to be producing a product for human consumption and they needed a piece of equipment that not only was safe and easy to use, but also easy to sanitize throughout the whole processing activity,” said Perry. “I worked with ADI when I was at General Mills and have known them since the early 90s. ADI also previously supplied PPB with a piece of equipment for their Ghana plant. “
ADI generously allowed PFS volunteers to bring ingredients into their facility to test make the product. This was vital to ensure the equipment worked efficiently and effectively before it was shipped to PPB. Perry explained, “When you’re working in Africa, there is one thing you tend to learn very quickly... if things don’t work right, it’s not going to be a quick fix overnight. It might be weeks until you get a new part and can fix something. Understanding that reality, it was extremely valuable that ADI let us bring ingredients like peanuts, milk powder and sugar into their facility to make peanut butter with the new equipment. Peanut butter is something you definitely don’t want splashed around your facility so we were really grateful that ADI opened up their facility for us to use as a small pilot plant.”
“We build food equipment for customers around the globe that we are very proud of, but I think this project probably made us feel even a little more satisfied than usual,” said Bill Olsen, the project manager from Anderson Dahlen. “This effort was particularly satisfying because of the end-user purpose. We were able to witness and participate in the production of some test products for the customer that we normally don’t get to engage with. The preliminary testing was important for us to conduct because it allowed validation of the system's mechanical and electrical control operations, while at the same time, validating the ability of the system to mix and process the specific ingredients into a finished product the client approved of.”
Even though ADI supplied PPB with a similar piece of machinery for their Ghana facility years back, this system was slightly different in process and scope and posed new challenges. “The end-user requested specific high amperage, quick-disconnect electrical connections for their eventual primary input power at their plant, which required slightly different termination and hookup hardware at the electrical control panels and drives. Because the system was also being shipped overseas, consideration also had to be given to the final sizes of various assemblies, as well as designing the parts of these assemblies with modularity to allow disassembly for nesting into shipping containers.”
After months of brainstorming, designing, fabricating and testing, the new processing equipment was recently containerized and shipped to PPB, where it will be assembled and go through additional testing. “We’re thrilled to have a custom piece of processing equipment that will be perfect for our RUTF product,” said Megan Manary, director of quality systems at Project Peanut Butter. “We’re so thankful for the PFS team, volunteers and Anderson Dahlen staff who donated over 200 hours and their expertise to this project. Through genuine partnerships like this, we’re able to continue our mission of improving food security across Africa and target vulnerable populations in need of more nutritious foods.”