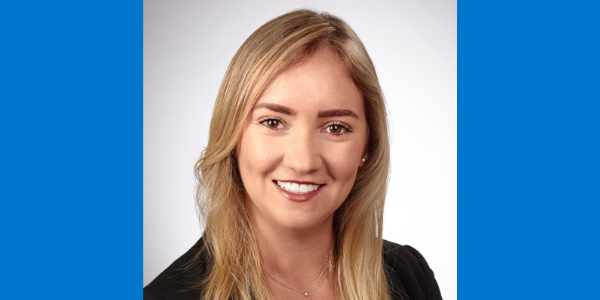
Improving Food Safety Through Global Partnerships
“I come from a developing country and I know how hard it can be for small businesses to get resources and support. I thought PFS was a great opportunity to give back and share some of the knowledge and skills that I’ve acquired over the years,” said Regina Barcena, senior manager of food safety & quality at The Hershey Company. Regina is currently volunteering with Partners in Food Solutions on a HACCP implementation project in Ghana.
PFS: Please tell us a little about your background.
RB: I am originally from Mexico and first started at Hershey as an intern there. I moved to our corporate office in Pennsylvania ten years ago and have had a few different positions including quality specialist, sanitation supervisor and quality engineer. I am currently the senior manager of food safety & quality at our Stuart Draft Plant.
PFS: Why did you decide to get involved with Partners in Food Solutions?
RB: I come from a developing country and I know how hard it can be for small businesses to get resources and support. I thought PFS was a great opportunity to give back and share some of the knowledge and skills that I’ve acquired over the years.
PFS: What has been the most rewarding thing about being a PFS volunteer for you?
RB: In general, the fact that I am able to improve the food safety culture of a developing country is very rewarding. Every year, there are millions of cases of foodborne illnesses, especially in low and middle-income countries. As a PFS volunteer, I delivered a good manufacturing practices training through video and demonstrated things like record-keeping and good hygiene practices to a client. I feel the work done by myself and the rest of the volunteers is raising food safety awareness and we’ve been able to reduce cases of foodborne illnesses.
PFS: Tell me more about the HACCP project you’re currently working on?
RB: The primary objective of the project is to develop a HACCP plan that will lead to an International Quality Certification. Gaining the additional certification will allow them to sell products in other countries and therefore increase their profits. It has been a very rewarding experience to work with volunteers from other companies like General Mills and Cargill. When we get together to help our client we are one team of experts, creating value for the final consumer. I consider this a perfect opportunity to be able to share my knowledge, learn from other experts and help people from other cultures and countries. Our next step is to train their 34 employees through a conference call and I am really excited to be part of this transformation.
PFS: What skills have you used/developed as a PFS volunteer?
RB: I’ve learned to be a partner. When I first joined PFS, I thought we were going to take on more of a consultant role. But, after the first meeting, I realized that I was going to learn just as much from them as they were from me. Volunteering with PFS and supporting African companies helped me realize that you can make big changes with small programs. I’ve been able to implement some of those learnings in my day job, and the learning and results have been fantastic.
PFS: How does the fact that Hershey supports PFS make you feel?
RB: Making moments of goodness is in Hershey’s DNA. I am grateful to work for a company that supports programs like PFS and allows me to develop my career in a global environment while at the same time supporting those in need.
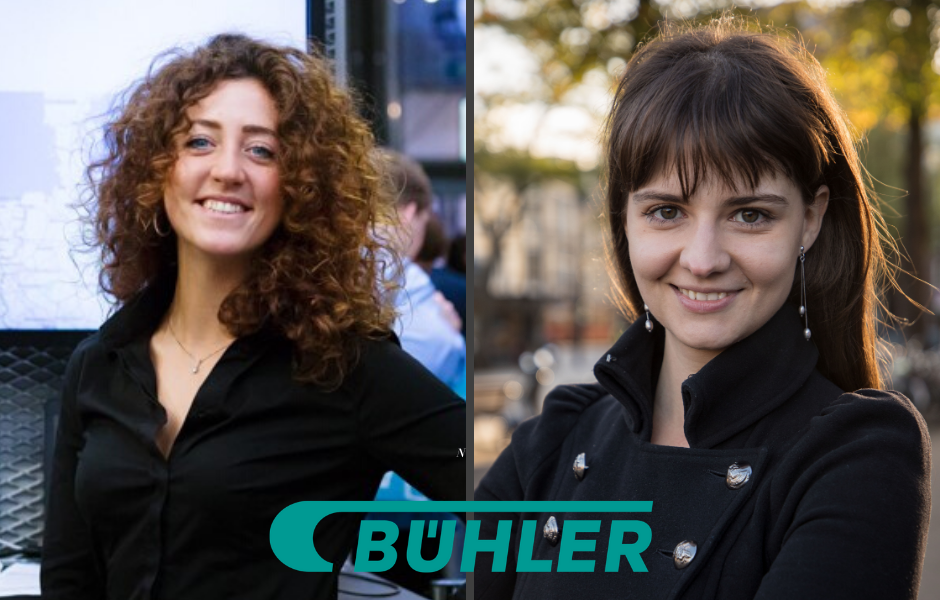
Two Bühler Volunteers Share Their Experience as Client Leads in 2019
We connected with first-time PFS volunteers, Camilla Cavalier and Sorana Ionita, to learn more about their recent experiences as client leads. When asked what she would say to someone who’s interested in joining PFS, Sorana, a Supply Chain Project Manager at Bühler, said, “If a certain project or company sparks your interest, either because you relate to their business or you have some of the skills required for the specific position, you should go for it! Even if the position doesn’t align with your day job’s description I would suggest you take a chance, volunteer as a client lead and enjoy the ride.”
PFS: Why did you decide to get involved with PFS?
CC: It didn’t take much for me to join. PFS aligns with my personal and professional interests, and since Bühler is an active partner I had some colleagues who were already involved. When I was asked to join a project I knew I wanted to get involved right away.
SI: I attended a training about cocoa farming in Ghana in early 2019 and that experience really opened my eyes to food production in Africa. After the training ended I knew I wanted to get involved in improving food security in Africa, but didn’t know how I could directly contribute as an individual. At the same time, a colleague introduced me to PFS and it was like the stars aligned – this was my chance to get involved with Africa’s food system.
PFS: Why did you choose to be a client lead for the company you work with?
CC: The client lead position for Valid Nutrition really aligned with my job at Bühler. I’m a project manager and already had experience working with remote and global teams so it seemed like a good fit for me. However, I didn’t have any experience in the project topic I was managing, which was a good challenge for me. I was exposed to quality lab design work that I would have otherwise never been exposed to in my day job at Bühler.
SI: My client, Fastizers Foods and Confectionery, was working on a food safety and quality control project, and a snack product development project involving cookies and biscuits. At Bühler, I am a supply chain project manager and do not work with food safety or product development. However, I am familiar with biscuit, cookie and waffle processing machinery, which helped me contribute in some areas of the projects with the client.
PFS: What’s your favorite part of being a client lead?
CC: I love coordinating the meetings and making sure everyone is getting value out of it. Sometimes it can be challenging to schedule calls with people from across the globe, but once we got the preliminary logistics worked out we were able to have fruitful discussions and I could keep the project moving forward through recap notes, delegating tasks, etc.
SI: I have really enjoyed working with people from such different backgrounds and cultures other than mine. I’ve been introduced to different perspectives and experiences that I may not otherwise get to interact with day-to-day. I’m always looking forward to my next status call!
PFS: What would you tell someone who is interested in becoming a PFS volunteer, but is hesitant to join?
CC: I would let them know that whoever joins as a volunteer is well supported by the PFS team. They’re available to answer your questions at any time and will be there to help you keep the project moving forward.
SI: If a certain project or company sparks your interest, either because you relate to their business or you have some of the skills required for the specific position, you should go for it! Even if the position doesn’t align with your day job description, I would suggest you take a chance, volunteer as a client lead and enjoy the ride.
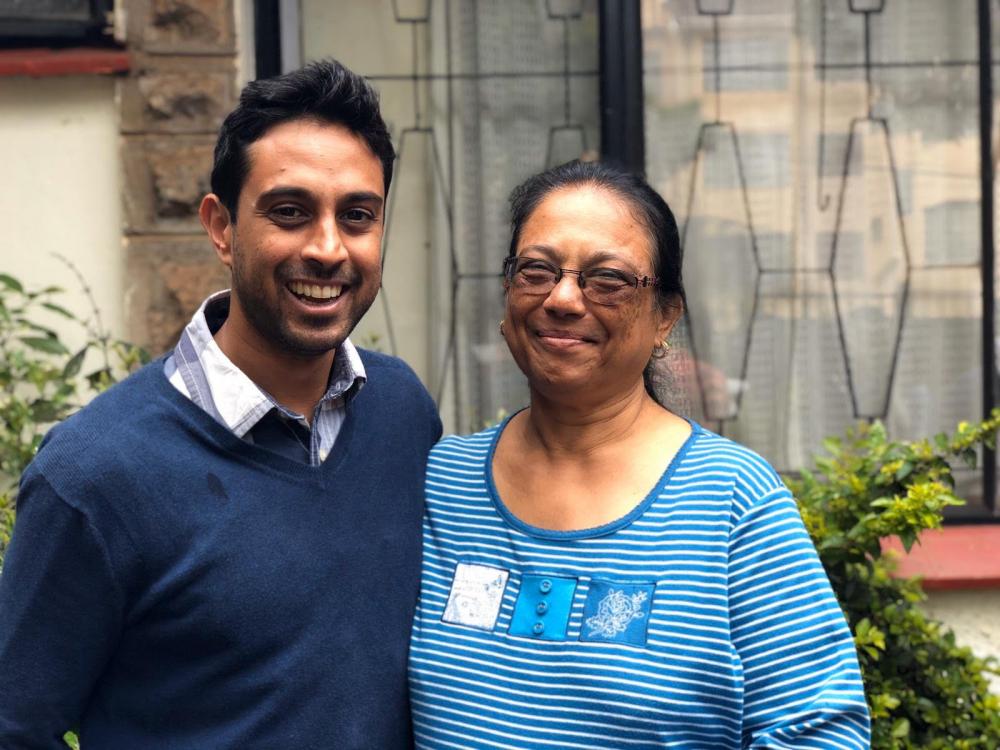
Family Business Finds Even More Success With Fruit Juice Reformulation
Being an entrepreneur is not always easy, but for Tropical Lush CEO, Adarsh Shah, it’s a labor of love. “About three years ago, we moved from a small production kitchen to our current premises, which is larger. Our current facility has allowed us to manage logistics better, increase storage and improve our growth trajectory. Managing a growing business in Nairobi has its challenges, but we love it.”
As a fresh fruit juice business with increasing demand from new customers, challenges pop up. One being shelf life. “We started gaining new customers and reaching people farther away from our production facility, and therefore needed to improve the quality of our product over a longer period of time.” To increase shelf life, Adarsh consulted PFS volunteers who provided recommendations for new juice formulations. “The shelf life of the product used to range from two to three days, but due to improved formulation, we’re now at four to five days. One of the best things from this past year is that we’ve received great feedback from our customers and we attribute that to the improved formulation that PFS volunteers helped us with."
Tropical Lush has been working with PFS for two years and has gone through a lot of changes over the years. “We’ve hired new, highly skilled managers, doubled production and increased the number of deliveries to our customers. Having Johnson from PFS as a resource has been very helpful. He’s been on the phone with us to help when issues arise; it’s almost like having a partner in our business that can help me think through things.” Tropical Lush plans to move into a larger production facility in the near future where they can continue to grow the business. Until then, Adarsh still makes time to deliver product himself to clients around town, “I really enjoy the day-to-day and it’s always fun to meet clients face to face.”
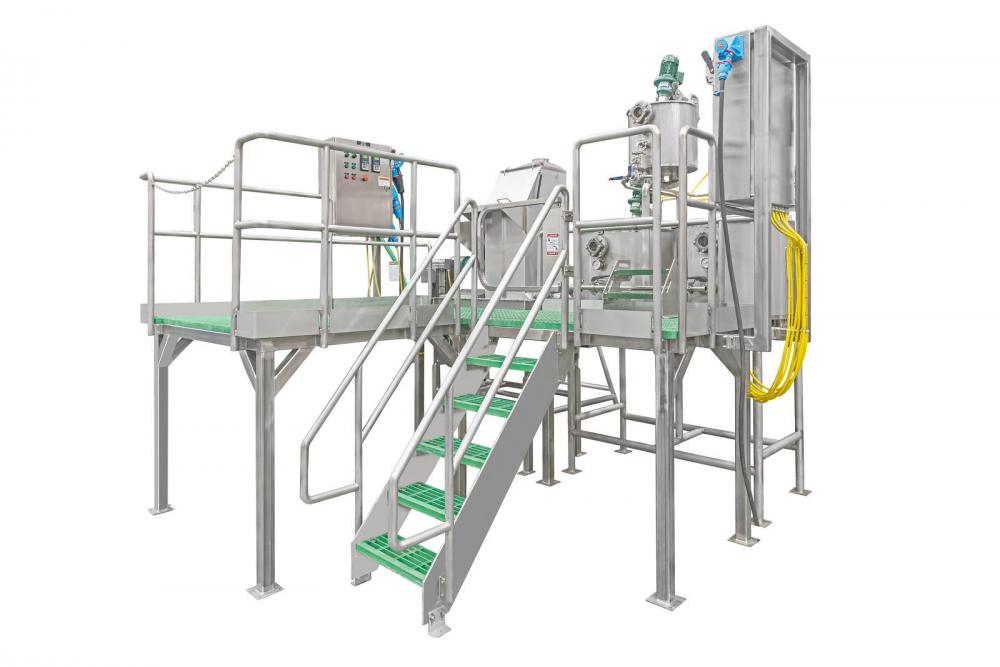
Custom Processing Equipment will Improve Production of Ready-to-Use Therapeutic Food in Côte d’Ivoire
Over 2 billion people around the world don't get adequate amounts of micronutrients in their diets like iron, vitamin A and zinc. Nutrient deficiencies can lead to stunted growth and life-long cognitive impairment in kids. Africa alone has the highest prevalence of undernourishment, with 20% of its population being affected. An important part of the PFS mission is to work with African food processing companies who provide healthy foods that support improved nutrition.
Project Peanut Butter (PPB), a nonprofit organization that seeks to advance the treatment of severe malnutrition through ready-to-use therapeutic food (RUTF) is one such client. RUTF is a nutrient-dense, locally produced peanut butter paste used for the treatment of severe acute malnutrition in children. PPB currently serves communities in Ghana, Malawi and Sierra Leone, and is expanding its operations to Côte d’Ivoire.
Partners in Food Solutions (PFS) and Project Peanut Butter have been working together since 2012 and have partnered on over 40 projects. Perry May, who retired from General Mills in 2015, has been volunteering on PPB projects since 2012 and has seen the impact of their work. “I really enjoy working with PPB. I’ve been involved with many of their projects and have seen a lot of business growth over the years and have even visited a PPB plant in Malawi. One of the current projects I am most excited about is their expansion project in Côte d’Ivoire,” Perry said.
With a new facility in Côte d’Ivoire, PPB will be able to reach a new population of people they didn’t have the opportunity to serve before. For the new plant, PPB was looking for recommendations to source a new piece of equipment to process their RUTF products.
After multiple discussions between PFS volunteers and PPB, they selected Anderson Dahlen Inc. (ADI), a custom design and manufacturing equipment builder based in Ramsey, MN, to design and build a RUTF processing system. “The reason we recommended them for the RUTF processing system was because we needed a vendor who had sanitary design for food equipment in mind. PPB was going to be producing a product for human consumption and they needed a piece of equipment that not only was safe and easy to use, but also easy to sanitize throughout the whole processing activity,” said Perry. “I worked with ADI when I was at General Mills and have known them since the early 90s. ADI also previously supplied PPB with a piece of equipment for their Ghana plant. “
ADI generously allowed PFS volunteers to bring ingredients into their facility to test make the product. This was vital to ensure the equipment worked efficiently and effectively before it was shipped to PPB. Perry explained, “When you’re working in Africa, there is one thing you tend to learn very quickly... if things don’t work right, it’s not going to be a quick fix overnight. It might be weeks until you get a new part and can fix something. Understanding that reality, it was extremely valuable that ADI let us bring ingredients like peanuts, milk powder and sugar into their facility to make peanut butter with the new equipment. Peanut butter is something you definitely don’t want splashed around your facility so we were really grateful that ADI opened up their facility for us to use as a small pilot plant.”
“We build food equipment for customers around the globe that we are very proud of, but I think this project probably made us feel even a little more satisfied than usual,” said Bill Olsen, the project manager from Anderson Dahlen. “This effort was particularly satisfying because of the end-user purpose. We were able to witness and participate in the production of some test products for the customer that we normally don’t get to engage with. The preliminary testing was important for us to conduct because it allowed validation of the system's mechanical and electrical control operations, while at the same time, validating the ability of the system to mix and process the specific ingredients into a finished product the client approved of.”
Even though ADI supplied PPB with a similar piece of machinery for their Ghana facility years back, this system was slightly different in process and scope and posed new challenges. “The end-user requested specific high amperage, quick-disconnect electrical connections for their eventual primary input power at their plant, which required slightly different termination and hookup hardware at the electrical control panels and drives. Because the system was also being shipped overseas, consideration also had to be given to the final sizes of various assemblies, as well as designing the parts of these assemblies with modularity to allow disassembly for nesting into shipping containers.”
After months of brainstorming, designing, fabricating and testing, the new processing equipment was recently containerized and shipped to PPB, where it will be assembled and go through additional testing. “We’re thrilled to have a custom piece of processing equipment that will be perfect for our RUTF product,” said Megan Manary, director of quality systems at Project Peanut Butter. “We’re so thankful for the PFS team, volunteers and Anderson Dahlen staff who donated over 200 hours and their expertise to this project. Through genuine partnerships like this, we’re able to continue our mission of improving food security across Africa and target vulnerable populations in need of more nutritious foods.”
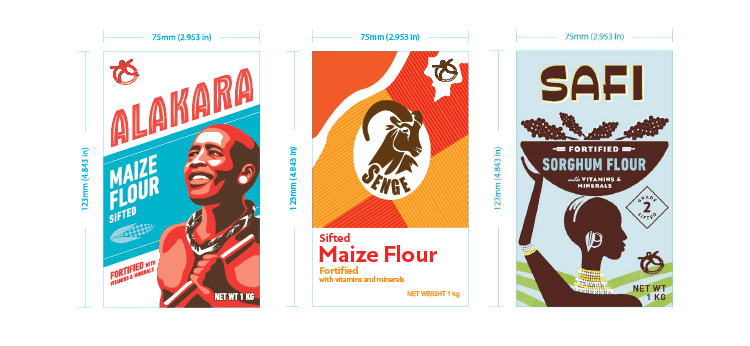
From General Mills to Hershey: How One PFS Volunteer Brought Global Opportunities to Her New Team
“As soon as I learned Hershey was involved with Partners in Food Solutions (PFS), I knew I wanted to get engaged,” said Mary Marette, a senior design manager at The Hershey Company. “In 2015, I just started a new job at Hershey and saw PFS as an opportunity to engage with the company, work with others and learn by doing.”
Mary initially got involved with PFS in 2008 when she worked at General Mills and was encouraged by her director to get involved. “My boss at General Mills was instrumental in getting our team involved with PFS. She really advocated for us to apply our expertise outside our day-to-day work and develop our skills in new and varied situations,” Mary, who now works at Hershey, strives to bring a similar experience to her team at Hershey.
Kelly McManus, an associate design manager and relatively new face at Hershey, had just started on Mary’s team when Mary suggested she get involved with a PFS project. “As I looked at Kelly, I saw someone who was new to Hershey and needed an opportunity to engage and stand out. I thought having Kelly join me on a PFS project would be a great way for her to meet people, get more engaged, do hands-on design work and most importantly develop her leadership skills,” Mary said. An opportunity arose for them to work together on a PFS project designing a logo and packaging for three Kenyan milling companies.
“This project was definitely something that got me out of my comfort zone and pushed me both professionally and personally,” Kelly said. “My day job primarily focuses on overall design strategy, so joining a PFS project allowed me to dust off my boots and get more involved in the actual design work. I had never worked on a global initiative before, so this was a completely new experience for me. The market is really different than the United States’ and we had to learn about their customers, shelf set, culture, etc. The project included many 6:00 am calls and asking a lot of questions like ‘What’s the difference between Maize and Sorghum?’ and ‘How is the product typically transported?’”
"To see a visual representation of our client's everyday lives, we requested pictures of their surroundings. We then received images from the client on WhatsApp of them in the middle of their field surrounded by goats. When we asked what the significance of the goats were we learned that ‘he goats’ represent pride, and it was a treasure to own a goat, especially when there was a drought. This type of real-time sharing and learning about a client and their culture first-hand made the project much more real.” And, Kelly said, it was a great opportunity to work with her supervisor on something completely new and different. “My boss was incredibly helpful throughout the whole project. Since she had participated in PFS projects before, she helped set the expectation and guided me through leading the creative direction for the three milling companies.”
With support from a Minneapolis-based creative agency, the project finished in November with four unique packaging designs. These designs will now be sent to a local printer in Kenya where they will be printed on packaging for the local market. “I am really proud of Kelly,” Mary said. “In addition to learning about a new client and getting back into hands-on design work, Kelly also had to think about where the client was with technology, what type of printers they had access to and what colors and types of branding would resonate with a culture that was different than her own. Her involvement in PFS truly illustrated her ability to deal with ambiguity, showcased her talent, revealed her desire to learn and engage, and highlighted her leadership skills. Kelly went above and beyond, all while using her skills to give back.” And while working with a client thousands of miles and many, many time zones away she also learned a little something extra about her colleague, “I also learned that Kelly is not a morning person.”